EU-funded BIOMOTIVE project seeking to develop bio-based products for automotive
EU-project BIOMOTIVE is seeking to develop bio-based products for automotive industry in order to replace non-biodegradable interior parts on vehicles with its biobased equivalent. The first results are promising and after industrial-scale tests planned in 2020, a bio-based thermoplastic polyurethane (TPU) should be available on the market at the end of 2021. The project sees the international […]
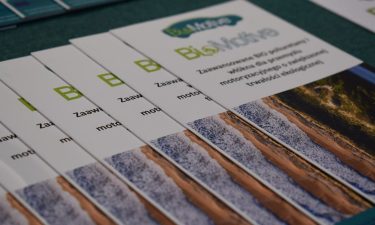
EU-project BIOMOTIVE is seeking to develop bio-based products for automotive industry in order to replace non-biodegradable interior parts on vehicles with its biobased equivalent. The first results are promising and after industrial-scale tests planned in 2020, a bio-based thermoplastic polyurethane (TPU) should be available on the market at the end of 2021. The project sees the international organization of public transport UITP among its partners.
The EU-funded BIOMOTIVE project aims to develop and produce new vehicle materials made largely from bio-based raw material that offer enhanced technical performance, an improved environmental profile and higher economic competitiveness.
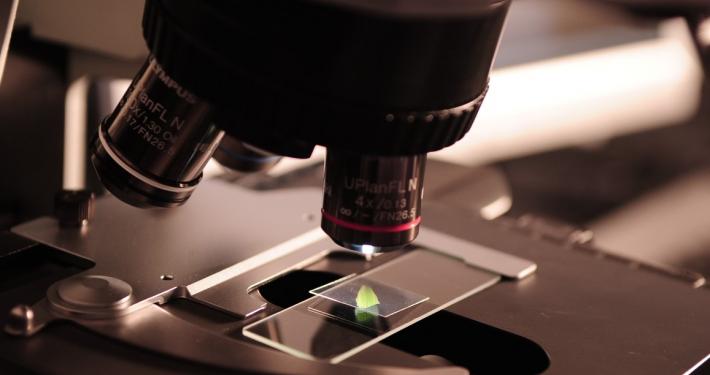
Towards market penetration of bio-based interiors
Funded under the European Union’s H2020 programme, BIOMOTIVE is a member of the Bio-based Industries Consortium (BIC) which represents the private sector in a public-private partnership with the European Commission, also known as the Bio-based Industries Joint Undertaking (BBI JU).
The BIOMOTIVE project counts 16 members from 8 European countries (research institutes, associations, universities and consultants). The project is coordinated by Selena, a Poland-based global player in the construction chemistry business.
BIOMOTIVE has the goal of paving the way towards the production and subsequent market penetration of bio-based automotive interior parts such as door handles, car-seats, and instrument panels, with the aim of replacing the fossil-based, non-biodegradable counterparts. The main focus is on car market, but some solutions could also be followingly adopted by commercial vehicles, including buses.
Within the project, innovative and advanced bio-based materials with increased bio-based content (60-80%) will be produced from renewable biomass feedstock (not in competition with food and feed), the project members point out. It is expected that such materials will demonstrate advanced properties in terms of resistance to fire, mechanical strength, and flexibility.
BIOMOTIVE: eliminate fossil fuels from the production process
Amongh the various renewable and biological products which are used in the BIOMOTIVE project we could mention wood, vegetable oils extracted from oilseed crops, and sugars from first and second generation by-products. All these materials will be used to eliminate fossil fuels from the production process of products such as flexible seating foam and bio-thermoplastic polyurethane (TPU), a rubber-like material.
Products developed within the BIOMOTIVE project are still undergoing initial tests, yet some of them have already been documented, the project members highlight. Continuous trials allow to determine the exact parameters of products, the content of bio-components, and define the product life cycle.
First result, a bio-based TPU rubber
Preliminary results are promising. For example, the recently developed formulation of the bio-based TPU rubber proved to consist for 67% out of bio-based content and can be mould injected into car parts using standard equipment currently used in automotive production. Also found was that this bio-plastic rubber can stretch up to 10 times its initial size. Research is being now directed towards easy processing of this material.
Other materials have been tested too: flexible foams for car seating have been developed with 60% bio carbon content and proved to have the same level of comfort as current car seating foams. Also, the fabrics that covered the bio-foams, were made from nearly 100% bio-based fabrics. These fabrics not only support the foam, giving it extra wear resistance, but also prove to increase the overall bio-content close to 70%.
The fabrics that have been produced within the BIOMOTIVE project, from cellulose fibres, are almost 100% natural and will replace the upholstery fabrics that have been so far made from synthetic materials, mostly polyester and elastane. The BIOMOTIVE bio-fabrics are currently undergoing further tests, which aim to improve their efficiency and examine their process ability.
BIOMOTIVE, not only automotive in the spotlight
Currently, the project is also in the process of testing the possibility of utilisation of the materials for other purposes. For example, bio-based materials such as TPU bioplastic and so-called 2K foam could be reprocessed into asphalt or insulation foam, or used as a raw material for the production of shoe soles. This shows that even though the main focus will remain the automotive industry, BIOMOTIVE products can be of wider use in the future.
The initial test results of BIOMOTIVE have been used for the preliminary analysis of the products’ Life Cycle Assessment (LCA). Further good news here: the initial LCA results for the car-interior part products based on BIOMOTIVE TPU rubber show that a reduction of over 70% of Global Warming Potential (GWP) can be achieved when using these materials compared to the currently used material.
The results of all the preliminary research, tests and measures indicate that the objectives of the project can be achieved and that BIOMOTIVE activities are going in the right direction. After industrial-scale tests planned in 2020, the bio-based TPU should be available on the market at the end of 2021.