Unleashing value with battery analytics in the mobility revolution, by PowerUp
Authored and sponsored by PowerUp As urban centers face mounting pressure to reduce greenhouse gas emissions, the electrification of bus fleets emerges as an increasingly efficient and sustainable urban planning initiative. Electric buses not only contribute to a diminished operational carbon footprint but also offer enticing benefits such as reduced operating costs (savings on fuel […]
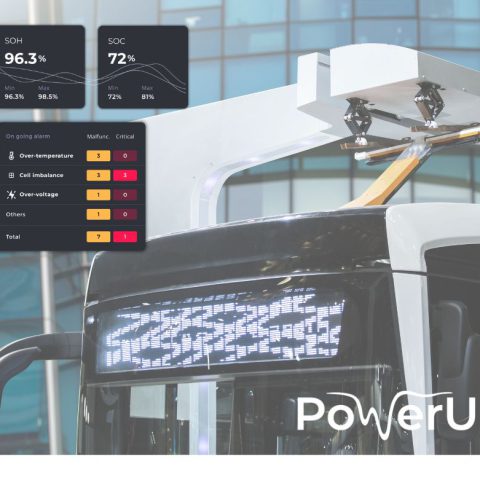
Authored and sponsored by PowerUp
As urban centers face mounting pressure to reduce greenhouse gas emissions, the electrification of bus fleets emerges as an increasingly efficient and sustainable urban planning initiative. Electric buses not only contribute to a diminished operational carbon footprint but also offer enticing benefits such as reduced operating costs (savings on fuel and maintenance expenses) and enhanced passenger comfort. Consequently, they are poised to play a pivotal role in the transition of fleet managers toward high-value, low-carbon operations.
Yet, the widespread adoption of electric buses faces a notable obstacle: the limited driving range in comparison to their internal combustion engine (ICE) counterparts. This constraint presents a significant challenge for fleet operators, whose success hinges on the optimized utilization of their assets.
However, far from accepting this limitation as inevitable, there are two scalable strategies that can be employed to surmount this hurdle:
- Implementation of intelligent charging infrastructure, tailored to the unique needs of buses and the strategic goals of fleet management.
- Rigorous monitoring of battery state-of-charge (SOC) and battery capacity degradation over time.
Reading between the lines, the effective execution of these strategies entails a comprehensive approach to battery data. This data is swiftly becoming the catalyst for controlling battery performance. It represents the key ingredient in transforming ‘black box’ batteries installed in buses into actionable insights that drive improved performance, reduced maintenance costs, and optimized battery life cycles.
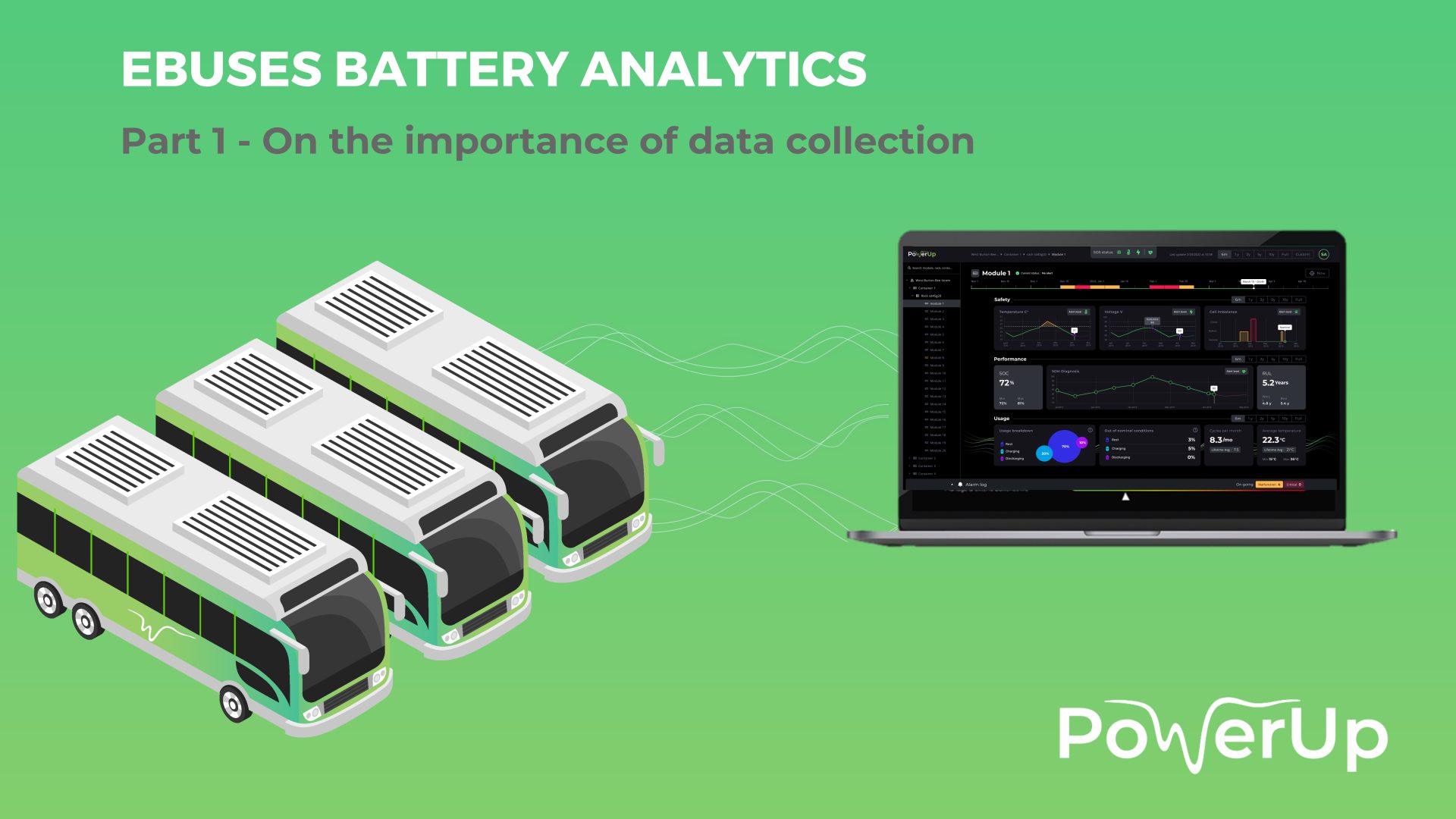
Data collection
To harness the power of battery data, fleet operators must first collect it effectively. There are three primary scenarios for collecting data from an electric bus’s battery and integrating it into the Intermodal Transport Control System (ITCS):
- Manufacturer-Installed Telematics: Some manufacturers equip their electric buses with telematic systems that gather data from various sensors, including the battery. This data is then accessible to fleet operators through APIs or central service portals, contingent on the manufacturer’s agreement.
- Third-Party Telematics: In the absence of manufacturer-installed telematics, fleet operators can turn to third-party providers who install external telematics modules on buses. These modules collect data from the vehicle interfaces, typically the Controller Area Network (CAN) bus, and send it to a central system. Fleet operators can access this data via APIs.
- On-Board Unit (OBU) Integration: Another approach involves using the fleet operator’s ITCS OBU to directly retrieve data from the vehicle interfaces and transfer it to the ITCS server for further processing.
Regardless of the data collection scenario, adopting open standards, such as the Telediagnostic for Intelligent Garage in Real-time (TiGR) protocol, or at least homogeneous way of collecting data is crucial. It ensures flexibility, prevents vendor lock-in, and facilitates interoperability among IT systems in public transport.
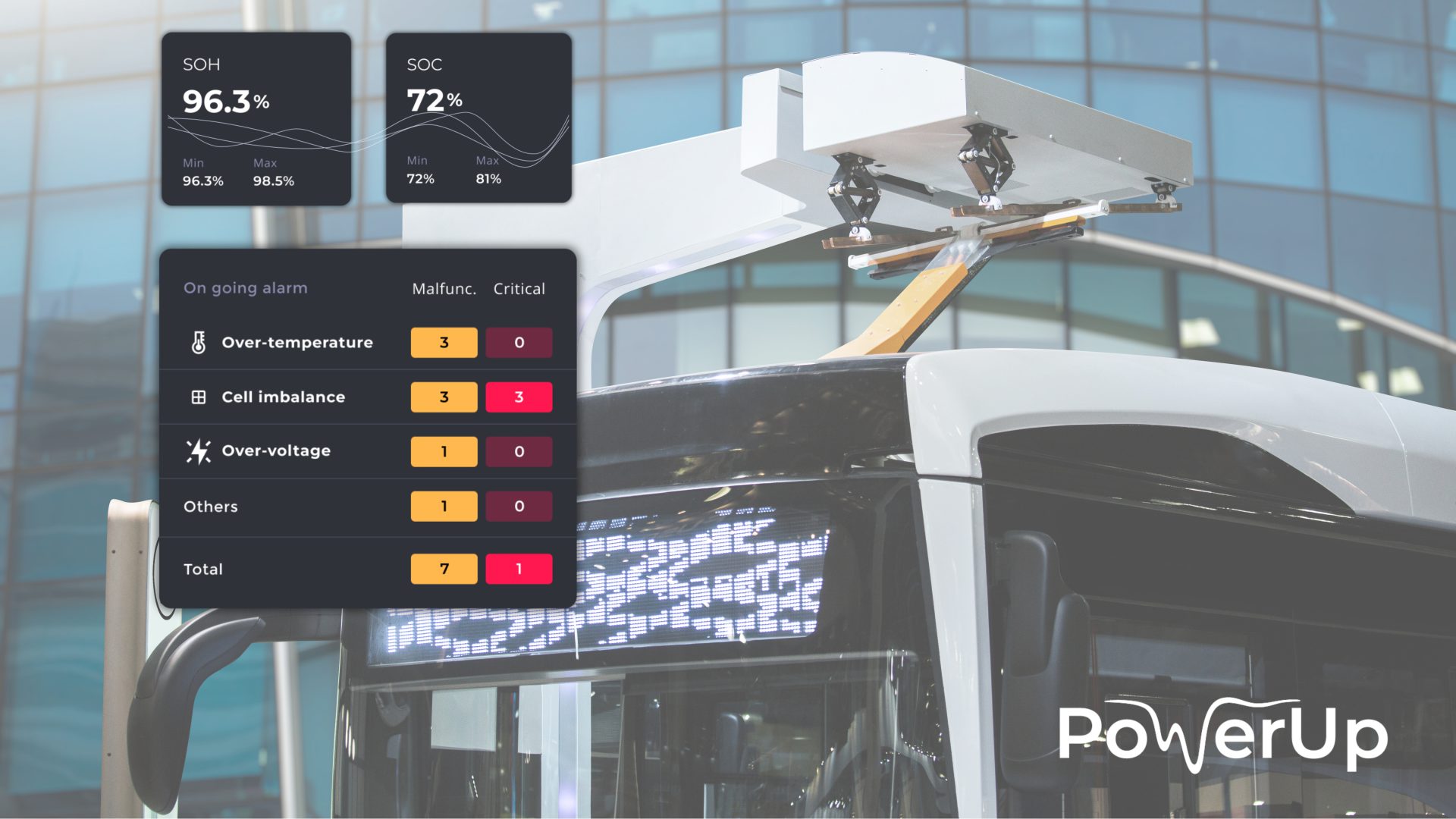
Data Requirements
Determining specific data requirements is essential for effective data collection. Key data points include voltage (U), current (I), and temperature (T), as these are fundamental for battery analytics. Minimum and maximum cell voltage and cell temperature are also critical for detecting cell imbalance-related anomalies. These parameters directly impact battery performance and capacity loss, enabling early detection and preventive action.
The upcoming article will explore how to enhance battery performance and capacity by relying on dependable and precise battery health and safety indicators.
Data Cleansing & Processing
Even with access to data, it must undergo rigorous cleansing and processing to yield valuable insights. Data quality and management face challenges related to data volume, errors in Battery Management System (BMS) measurements, and communication failures on electric buses. The raw battery operation data is filtered, standardized, and validated, with checks for anomalies and data gaps based on battery usage profiles. The result is a reliable dataset that fuels degradation and safety algorithms.
- Effective data cleansing and processing enable smooth algorithm performance, leading to:
- Reduced operation and maintenance costs
- Extended longevity of electric bus fleets by minimizing downtime
- Early detection of battery hazards, preventing potential fire incidents
Battery Insight® cloud-based battery analytics strives to deliver these benefits.
Conclusion
Electric buses are the future of urban transportation, offering sustainability and cost-efficiency benefits. To unlock their full potential, fleet operators and integrators must prioritize battery data collection and analysis:
- Gain access to the right data through telematics systems or onboard units’ providers.
- Promote global IT communication standards for interoperability.
- Employ high-quality data cleansing processes, to ensure algorithms receive accurate and reliable data.
- Battery analytics is key to optimizing electric bus fleet performance and ensuring a sustainable and low-carbon future for urban transportation.
In the upcoming article, we will delve into how battery analytics can extract value from battery data. We will present real-world examples demonstrating how battery analytics can enhance your financial performance and grant you a competitive advantage in the ever-evolving mobility market.