TSA: A glance on present and future of electric drives for e-buses. Our interview with Innovation Manager Markus Neubauer
Over 60 years experience in the railway motor’s business since a few years ‘poured’ into the electric bus market in the last decade. Austrian company TSA (Traktionssysteme Austria) has provided so far electric motors for vehicles operating in more than 60 countries all over the world. The company is known for its solutions for both rolling stock […]
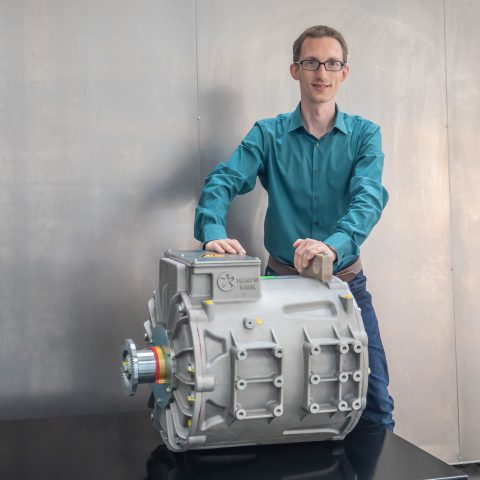
Over 60 years experience in the railway motor’s business since a few years ‘poured’ into the electric bus market in the last decade. Austrian company TSA (Traktionssysteme Austria) has provided so far electric motors for vehicles operating in more than 60 countries all over the world. The company is known for its solutions for both rolling stock and commercial road vehicles.
But which are the future challenges associated with electric drives? How to choose the best solution for each application? Which innovation should we expect in the electric motor market? We asked those – and many more – questions to Markus Neubauer, Innovation Manager at TSA.
The company is headquartered in the Austrian town of Wiener Neudorf, nearby Vienna. And it has international representations all over the world: USA, India and China.
If your partner comes along with a good idea, why not change the motor design if you can get more out of the system? If you take a look at the developments of semiconductors and control systems, there are new, very interesting concepts on the way, and we try to support them by realizing a solution which is not on the market by now. And in the end you can indeed have a system, where there is no need for a trade-off between size, performance and efficiency anymore, but where you can increase performance and efficiency at the same time at the same machine size. That requires very close collaboration with our partners and customers. But that’s the fun part of our job – to work as specialists together with specialists.
Markus Neubauer, Innovation manager at TSA
TSA: designing and manufacturing electric motors is our passion and our business
Markus Neubauer, may you give us a picture of your company?
«We design and manufacture electric motors both for the railway sector as well as for commercial road vehicles including Ground Support Equipment. We have been supplying electric motors for electric buses like trolleybuses for quite a long time already. Right at the moment we see that the market for electric buses is exploding. Many different players are trying to enter the market. And because of the climate protection targets to significantly reduce the carbon emissions, more and more electric buses will be required in the next few years. This means that our activities in the bus field are bound to grow. We provide innovative solutions for urban electric mobility around the world».
Within TSA, are there connections between the Road and Railway divisions?
«All our departments work closely together. The interdepartmental communication enables us to develop and implement solutions and ideas faster and more efficiently. That’s why we can offer one-stop solutions and guide our customers every step of the way through development and engineering, manufacturing and inspection as well as customer service for the entire product lifetime of our traction drives. The road sector is served by a dedicated sales team with specialists in this sector. Today, railway and road motors are built on the same production line, but the market is growing fast and we are getting prepared for different options in the future».
Your company designs and manufactures both induction motors and permanent magnet motors. What are their advantages and disadvantages?
«The induction motor is based on a very simple and robust technology. It can be used for different applications, including traction. But it might not always be the best solution, and each has its own advantages and disadvantages. It depends on the customer’s needs and requirements to choose the most suitable concept. The permanent magnet machine is a very attractive alternative as well. With TSA, you don’t need to select the supplier depending on your vehicle concept. If you want to implement your solution with an induction machine, we can support you in the same way as when you choose the permanent magnet machine as your preferred option. You might prefer the induction machine if you have longer coasting phases in your application, or the permanent magnet machine if you accelerate and brake very often, or if you need a very high peak torque density or efficiency. We have long experience with both types of machines, concerning the design as well as the manufacturing».
To date, the permanent magnet machine is the most common choice when it comes to e-buses…
«That’s true. When we look at road applications, PM machines are dominant. These permanent magnet motors are not all of the same type, as there are multiple variants – different magnet arrangements, permanent magnet assisted synchronous reluctance machines or even the axial flux machine».
You can find our self-ventilated induction motors in trolleybuses in Salzburg, Austria, while the forced ventilated induction motors of different size drive trolleybuses in cities like Dayton (Ohio), Zurich, Montreux, Verona, Guadalajara, Bologna, and Bucharest. Liquid-cooled permanent magnet motors are part of several new projects of drive systems for electric buses. We even have designed a prototype of an air-cooled permanent magnet bus motor. There are still ways to build the machines smaller, quieter and more efficient, although the technology is already on a high level.
Markus Neubauer, Innovation manager at TSA
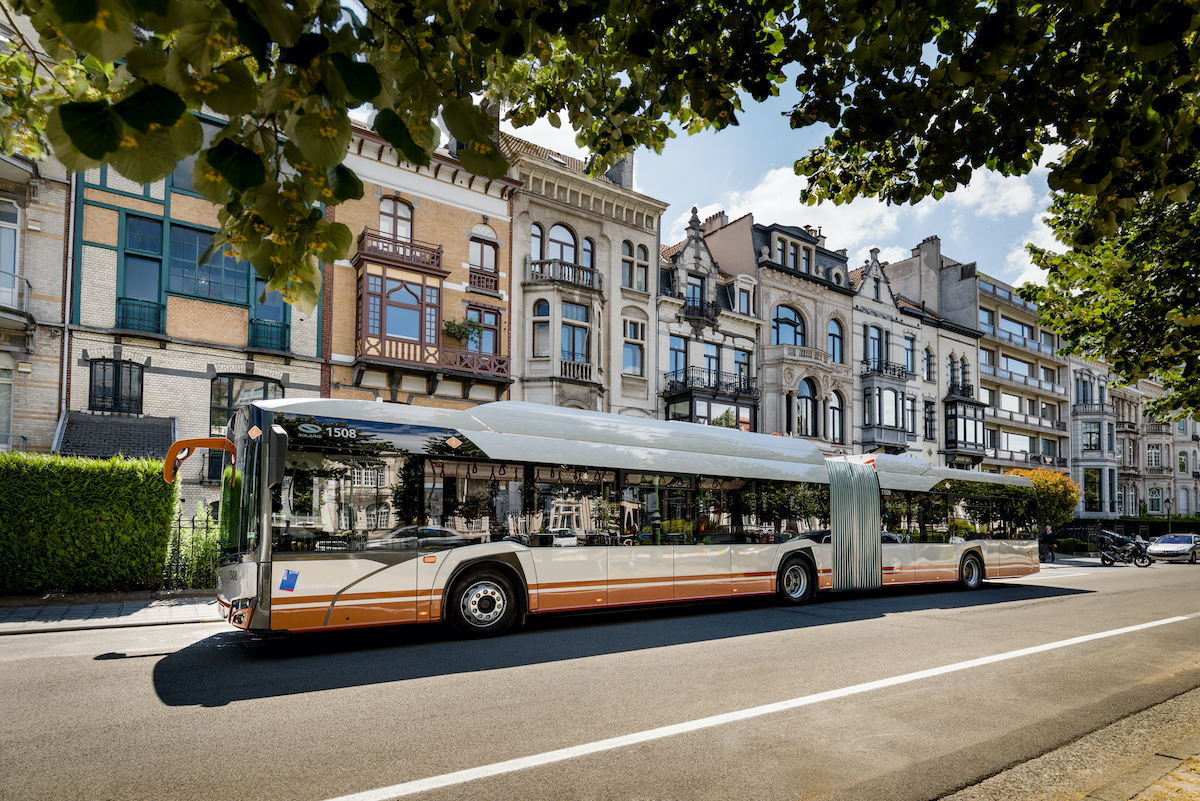
Many ways of cooling motors
The cooling concept is a crucial part of the electric motor. Can you give us an insight of your cooling concepts?
«Besides the common liquid cooling, we have very long experience with air-cooled traction motors of different types: self-ventilated and forced-ventilated, open or encapsulated. Each system has its own pros and cons concerning cooling capability, noise emission, complexity of the cooling arrangement, ease of maintenance and protection against dust, dirt or water. As a result, you can find our self-ventilated induction motors in trolleybuses in Salzburg, Austria, while the forced-ventilated induction motors of different size drive trolleybuses in cities like Dayton (Ohio), Zurich, Montreux, Verona, Guadalajara, Bologna, and Bucharest. Liquid-cooled permanent magnet motors are part of several new projects of drive systems for electric buses. We even have designed a prototype of an air-cooled permanent magnet bus motor. There are still ways to build the machines smaller, quieter and more efficient, although the technology is already on a high level».
Future electric bus models will not be traditional buses with an electric motor replacing the combustion engine. The new generation of electric buses will be increasingly designed around the electric drivetrain. How do you think this may change the market trends in terms of powertrain?
«In the near future, we will see a lot of different kinds of traction drives. There are many different possibilities where to place an electric motor in an electric bus. The requirements regarding weight and noise emissions will be ever more demanding in the future. Recently we built one of the lightest TSA motors so far which we perfectly synchronized with the vehicle’s overall system. For building the prototype, we used modern 3D printing and also incorporated results from various research projects.
Many players bring different concepts to the market, but in the end quality and reliability will prevail. Vehicles will offer a totally new travel experience to the passengers during the ride. I think this is a good thing as, at the end, it serves the customer, and I mean the end customer: the passenger. Public transport users want good accessibility to the vehicles, no steps to climb to reach the seats, and drive technology will be aiming to accomplish these needs».
Which innovations can we expect in the electric motor field?
It looks like there is a kind of a ‘challenge’ in the e-bus drive market between central drives and e-axles…
«And there are other options than those two. Concepts with motors near the wheels but in other arrangements, concepts without gearboxes and others with one-stage, two-stage or three-stage gearboxes».
Remember that a bus or a commercial vehicle cannot be compared to a car, as a bus is usually used continuously for more than 12 hours a day, 7 days a week and can reach a mileage of one million kilometres during its lifetime. And our motors are definitely prepared for that. As we come from the railway business, our motors are known for having a very long lifetime.
Markus Neubauer, Innovation Manager at TSA
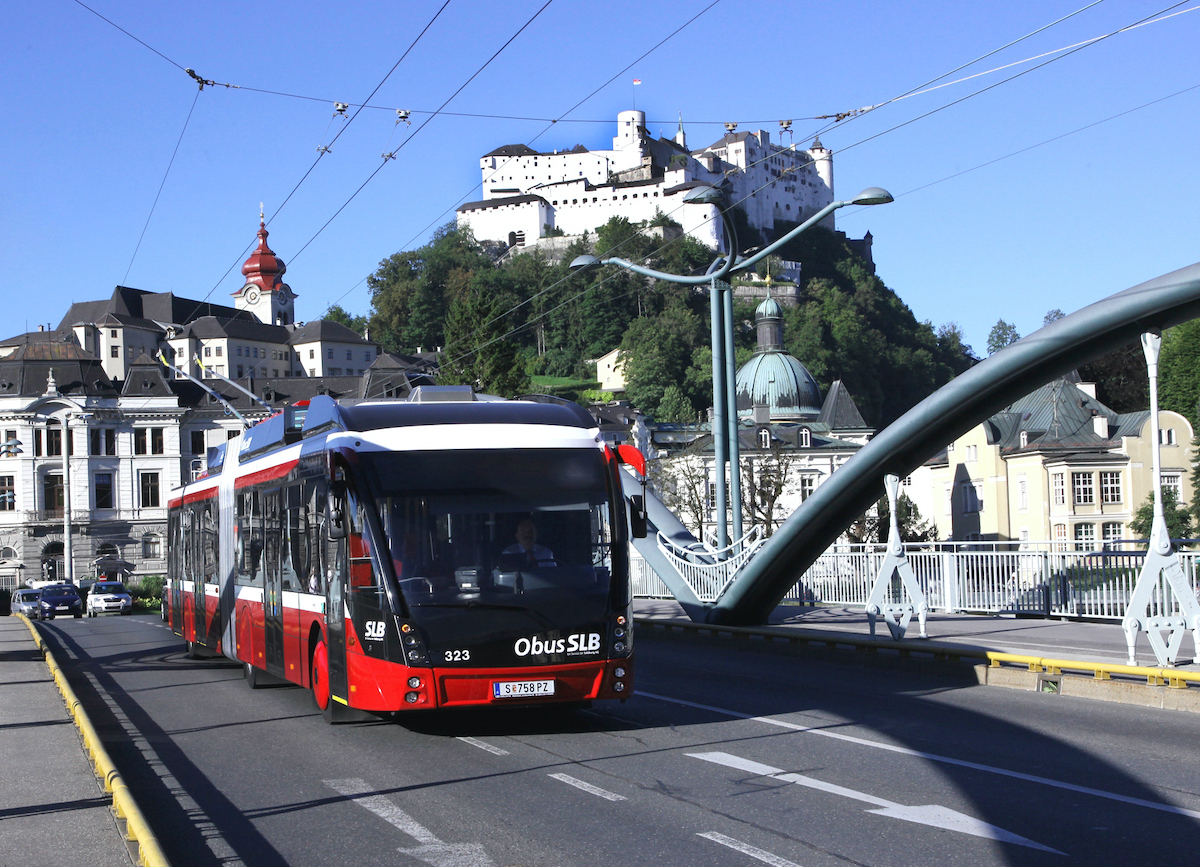
The electric machine is not a new invention. Are there still innovations to be expected?
«The electric machine consists of components that have been tried and tested for several decades already. What we see at the moment is that different concepts are used. But if we look at the whole driveline, for instance motor and inverter, there are now interesting options. Typically today a classic electric machine has three phases, controlled directly by the inverter. But this is not mandatory. If your partner comes along with a good idea, why not change the motor design, if you can get more out of the system? If we look at the whole driveline, for instance motor and inverter, there are now interesting options. Regarding the semiconductor and control development, there are new, very interesting concepts on the way, and we try to support them by realizing a solution which is not on the market by now. And in the end you can indeed have a system, where there is no need for a trade-off between size, performance and efficiency anymore, but where you can increase performance and efficiency at the same time at the same machine size. That requires very close collaboration with our partners and customers. But that’s the fun part of our job – to work as specialists together with specialists.
I think the real innovations will be on one hand between inverter and motor and on the other hand on the mechanical side. The questions are: How is the motor arranged? Where is it placed in the bus? How is it connected to the wheels or to the axle? To which extent can we reduce the weight and size of the motor? Another source of innovations may come from new materials».
When we talk about core competence, what do you think is important for an electric machine to work properly?
«One very important part of the electric machine is definitely the insulation system. Many disciplines meet there – electric and mechanical engineering, chemistry and manufacturing technology. We are proud to have an insulation system for electric machines in the portfolio which offers one of the highest thermal classes available nowadays – Class 250. This enables very high performance and power density, and at the same time ensures an exceptionally long lifetime. The experience of developing such a system also impacts other, more affordable options of insulation systems of our portfolio. Remember that a bus or a commercial vehicle cannot be compared to a car, as a bus is usually used continuously for more than 12 hours a day, 7 days a week and can reach a mileage of one million kilometres during its lifetime. And our motors are definitely prepared for that. As we come from the railway business, our motors are known for having a very long lifetime».
There is a future ahead: Will Hyperloop be part of it?
Are there any specific challenges related to hydrogen buses, from your perspective as a motor supplier?
«Not really: Customers can use the same electric motor and driveline with battery-electric buses and with fuel cell buses».
Today the debate around e-buses takes for granted that we are talking about city buses. In the future, the pace of electrification will also reach intercity and coach segments, maybe under the fuel cell hydrogen technology’s domain. Will you have to develop new products for this long-distance applications? Or is TSA ready for such a challenge?
«TSA is well prepared because we have been serving the intercity market in the railway sector for over 60 years so far. We know how to deal with long distance travels from the technical design point of view. The driving cycle is completely different: while an urban bus accelerates and brakes very often, the driving cycle of an intercity bus contains long coasting phases. So also the technical solution is different. We understand these requirements and know how to set measures for the design of the machine and the gearbox. Besides general decisions like motor and gearbox technology, there are lots of different technical parameters you can tune».
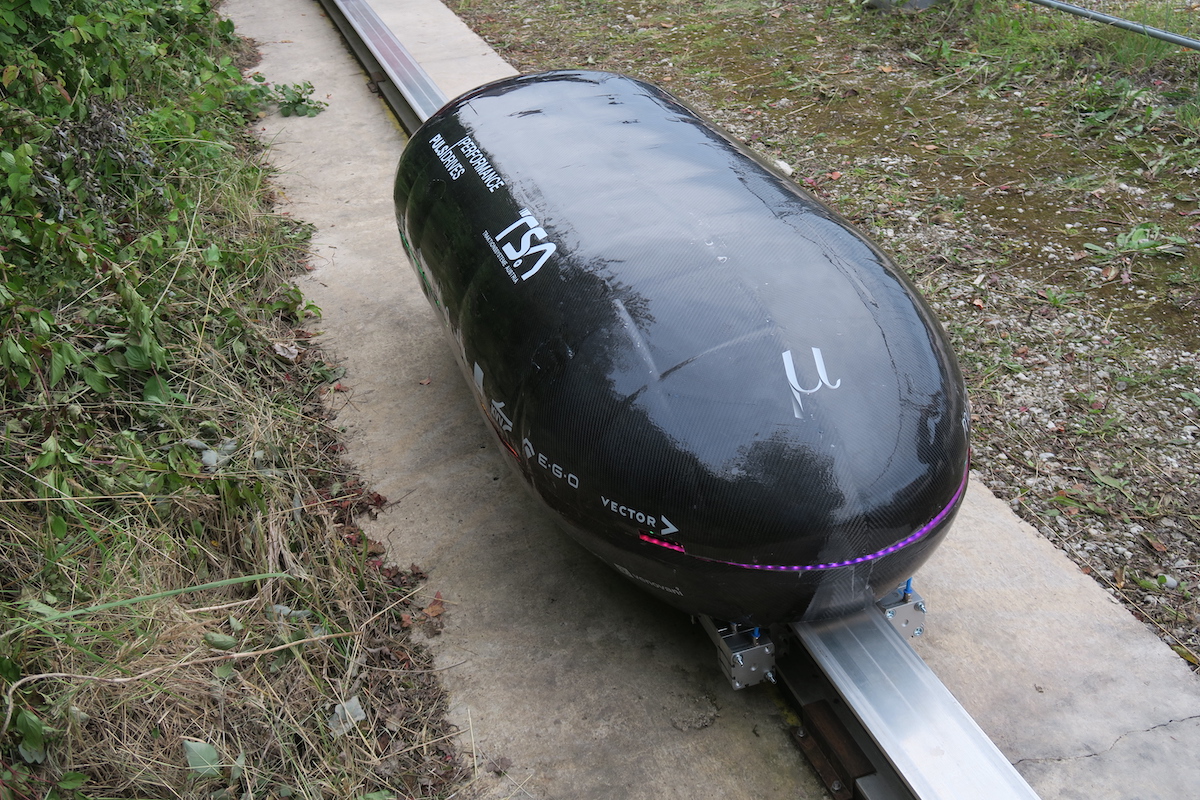
What is your most innovative product at the moment?
«One of them is the linear induction motor for a Hyperloop vehicle. TSA has a cooperation with a team closely related to the KIT (Karlsruhe Institute of Technology). The motor we built for this project is so special because it is used not only for propulsion but also for levitation. Sara Luchian, Director of Passenger Experience at Virgin Hyperloop, was the first passenger of a hyperloop system. At the European Hyperloop Week 2021, she said about current transport systems: “We are addressing the need for transport of the 21st century with solutions from the 20th century“. There might be the need for a new kind of transport. At the moment, the hyperloop concept is at an early stage of development. There are many open issues and critical questions. Anyway – to be part of such an innovative project leads us to develop new technologies. And maybe in the future, these technologies will power new applications and drive our future modes of transport».