On the reasons behind e-buses (and EVs) fires and how to decrease risks (the problem is smaller than one might think)
A contribution by Prof. Paul Christensen, Claudius Jehle, Alex Johns, Paul Markham published on February 2022 issue of Sustainable Bus magazine. The 1950s through 1980s saw a drive towards increasing the energy density and size of steam turbines from c. 150MW to 600MW – and several severe incidents due to early-stage design shortcomings are well […]
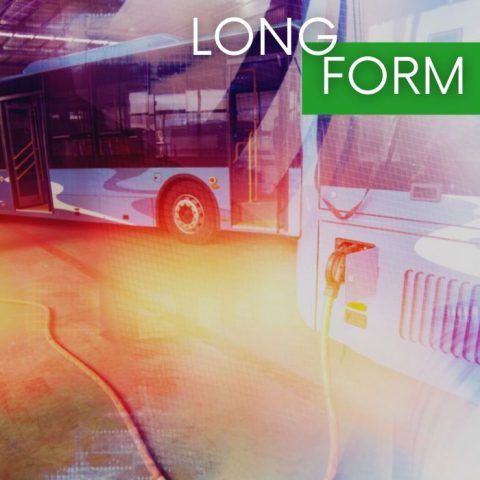
A contribution by Prof. Paul Christensen, Claudius Jehle, Alex Johns, Paul Markham published on February 2022 issue of Sustainable Bus magazine.
The 1950s through 1980s saw a drive towards increasing the energy density and size of steam turbines from c. 150MW to 600MW – and several severe incidents due to early-stage design shortcomings are well recorded1. But, as in every developing industry, each development is likely to go through, and undergo at times a painful cycle of continuous leaning and improvement.
In the oil and gas industry, the IOGP norms successfully define clear barriers and procedures intended to mitigate risks of early stage technology. But not only in this industry it is best practice to collect, monitor and transparently share and discuss information on incidents and failures to fuel an improvement process – one that brought such turbines to maturity.
Electric vehicles fire: batteries and reasons
What does that example tell us about electric vehicles? That (a) inexcusable events like fires are to some extent expectable and (b) can be overcome if there is transparency on root causes.
As experts from academia, firefighter training, diagnostics and insurance, we are in close contact with the stakeholders every day and will thus not marginalize the severe challenges they face after a fire, such as in Stuttgart2 or Hannover3. A few days ago, a RATP e-bus (by BlueBus) caught fire in Paris. Rather, we want to raise general awareness of the scope of the problem and present mitigation strategies.
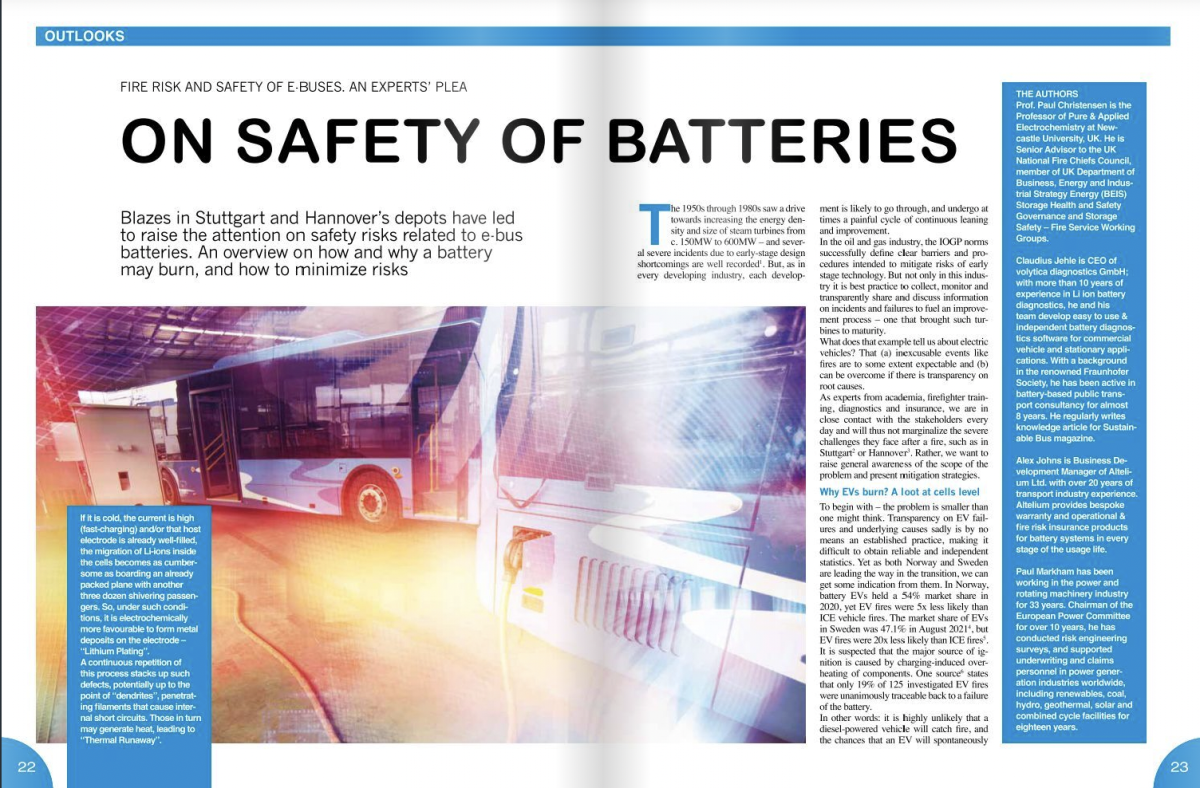
Why EVs burn? A loot at cells level
To begin with – the problem is smaller than one might think. Transparency on EV failures and underlying causes sadly is by no means an established practice, making it difficult to obtain reliable and independent statistics. It is suspected that the major source of ignition is caused by charging-induced overheating of components. One source4 states that only 19% of 125 investigated EV fires were unanimously traceable back to a failure of the battery.
The conditions that facilitate plating are only partially controllable by a vehicle’s battery management system. It is the operator’s responsibility to monitor and foster their batteries, just like careful storage, handling and sensible monitoring of flammable liquids is unquestioned best-practice.
Electric vehicles fire: understanding ‘lithium plating’
Generally speaking, a Li-Ion battery can be regarded safe. “Self ignition” can, if at all, only be assumed if internal microscopic defects accumulated to critical levels. In simple terms Li-ions travel from one pole to another inside a cell, while electrons take that journey through the electric circuit of the vehicle. Under good conditions, the ions migrate into the opposite electrode to be reunited with the well-travelled electrons. Yet if it is cold, the current is high (fast-charging) and/or that host electrode is already well-filled, this migration becomes as cumbersome as boarding an already packed plane with another three dozen shivering passengers. So, under such conditions, it is electrochemically more favourable to form metal deposits on the electrode – “Lithium Plating”.
A continuous repetition of this process stacks up such defects, potentially up to the point of “dendrites”5, penetrating filaments that cause internal short circuits. Those in turn may generate heat, which is vital for speeding up chemical processes, leading to even more heat and gases being generated – a self-sustaining process called “Thermal Runaway”. Such a situation becomes ballistic in less than 5 minutes, eventually violently venting gases in the form of electrolyte-soaked, thick white vapor clouds6. These clouds can ignite into long, flare-like flames, flash fires or even an explosion.
Note: the conditions that facilitate plating are only partially controllable by a vehicle’s battery management system. It is the operator’s responsibility to monitor and foster their batteries, just like careful storage, handling and sensible monitoring of flammable liquids is unquestioned best-practice.
A more bespoke procurement philosophy that puts TCO over CAPEX and goes away from unnecessary long-range requirements – everywhere this is financially and legally possible – will have a strong impact not only on longevity, economic feasibility and safety, but also lower costs in the long run.
Electric vehicles fires: a techno-economical perspective
One of the greatest advantages of EVs is not only their expected environmental impact, but their potentially superior total cost of ownership (TCO) – that is, low fuel and maintenance costs and long lifetime, if maintained well. This can naturally be achieved by bringing CAPEX/OPEX down, or lifetime up, or ideally both. Alas, in the last decade or so, the demand-side was unilaterally focused on CAPEX reduction. This is partially due to long-established (or mandated) procurement philosophies, but also due to a lack of leasing or other advanced financing opportunities, as we outlined in the last edition of Sustainable Bus magazine.
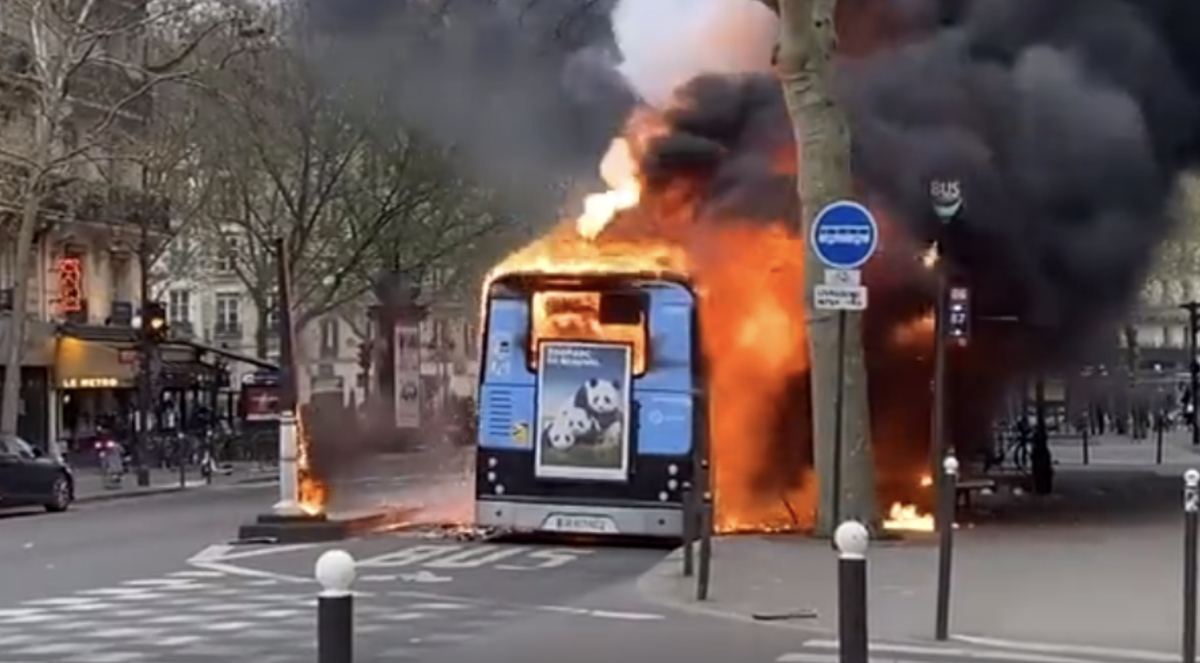
This prioritization of a “race to the bottom” in price reduction over lifetime, in conjunction with the universal and largely unquestioned hunger for range and fast-charging capability and their demonstrated adverse effects on safety, logically went at the cost of longevity and safety. The notorious secretiveness around the known and (of course) all the unknown EV fires in turn does nothing to help improve the situation.
How can risks of EV fires can be decreased?
Equipment barriers. Long-range, fast-charging-able assets at the lowest price might bear issues with longevity, availability and also safety. A more bespoke procurement philosophy that puts TCO over CAPEX and goes away from unnecessary long-range requirements – everywhere this is financially and legally possible – will have a strong impact not only on longevity, economic feasibility and safety, but also lower costs in the long run.
Construction measures. Bringing in dedicated Li-ion fire risk experts into the depot design and construction process must become customary. An increased awareness for sharing experiences about, circumstances of and reasons for past incidents will hopefully also lead to a continuous improvement process in the industry – this demands a willingness to share lessons-learned.
Human factors. All people must understand the basic physical principles and take heed of the “dos and don’ts” – vehicle drivers, maintenance personnel to planners, purchasing and bookkeeping departments, need to be made aware via trainings and continuous education. Just as one doesn’t smoke next to the gas nozzle, “cold fast-charging” must be avoided wherever possible. There must be an understanding that not everything that is possible or allowed is necessarily advisable or harmless, but can in fact be detrimental.
Proper management and due use of an asset. Permanent knowledge of battery safety and quality status, indications about preventive lifetime and risk optimization potentials and suitable early-warning systems of batteries, vehicles and infrastructure must and will become standard, given the virtually nonexistence of visual or other battery checks. A well-managed portfolio will also reduce fire and operational insurance costs and have a substantial lifetime and TCO impact. It is becoming common for operators to demand periodical asset portfolio quality reports from the OEMs – a step into the right direction.
All stakeholders – the whole industry, operators, users, OEMs and manufacturers, insurance, leasing and banking companies, policy makers and industry associations – must all stand up for sharing information transparently to facilitate a safe and economical transition that can keep up with international competition. Christensen, Jehle, Johns, Markham
1 Bush, S.H., 1978, Nuclear Safety, “A reassessment of turbine generator failure probability”, Vol.19, No. 6, p 681 – 696.
2 https://www.stuttgarter-zeitung.de/inhalt.grossbrand-in-stuttgarter-busdepot-ausgebrannter-bus-geborgen.28e79888-2001-46a6-989a-d5fadcec2ba9.html
3 https://www.focus.de/auto/ratgeber/sicherheit/braende-elektrische-busse-e-busse-nach-grossbrand-vorsichtshalber-stillgelegt_id_13371120.html
4 https://www.evfiresafe.com/ev-fire-global-timeline (24 of 125 investigated fires were unanimously traced back to battery failure)
5 Cf. Latin dens, „tooth“ (cf. dentist). Note that there are also other bad effects, but for the sake of simplicity we limit ourselves here
6 This vapor cloud consists of droplets of electrolyte, hydrogen (ca. 30-50%), oxygen, carbon monoxide, carbon dioxide, hydrogen fluoride, hydrogen chloride, hydrogen cyanide, ethane, methane and other hydrocarbons, sulphur dioxide and nitrogen oxides, A. R.Baird, E. J. Archibald, K. C. Marra and O. A. Ezeko, “Explosion hazards from lithium-ion battery vent gas”, J. Power Sources, 446 (2020) 227257, https://doi.org/10.1016/j.jpowsour.2019.227257 or P. A. Christensen, Z. Milojevic, M. S. Wise, M. Ahmeid, P. S. Attidekou, W. Mrozika, N. A. Dickmann, F. Restuccia, S.M.Lambert and P.K.Das, “Thermal and mechanical abuse of electric vehicle pouch cell modules”, Applied Thermal Engineering, 189 (2021) 116623, 16pp
THE AUTHORS
Prof. Paul Christensen is the Professor of Pure & Applied Electrochemistry at Newcastle University, UK. He is Senior Advisor to the UK National Fire Chiefs Council, member of UK Department of Business, Energy and Industrial Strategy Energy (BEIS) Storage Health and Safety Governance and Storage Safety – Fire Service Working Groups.
Claudius Jehle is CEO of volytica diagnostics GmbH; with more than 10 years of experience in Li ion battery diagnostics, he and his team develop easy to use & independent battery diagnostics software for commercial vehicle and stationary applications. With a background in the renowned Fraunhofer Society, he has been active in battery-based public transport consultancy for almost 8 years. He regularly writes knowledge article for Sustainable Bus magazine (the Battery Cycle series).
Alex Johns is Business Development Manager of Altelium Ltd. with over 20 years of transport industry experience. Altelium provides bespoke warranty and operational & fire risk insurance products for battery systems in every stage of the usage life.
Paul Markham has been working in the power and rotating machinery industry for 33 years. Chairman of the European Power Committee for over 10 years, he has conducted risk engineering surveys, and supported underwriting and claims personnel in power generation industries worldwide, including renewables, coal, hydro, geothermal, solar and combined cycle facilities for eighteen years.